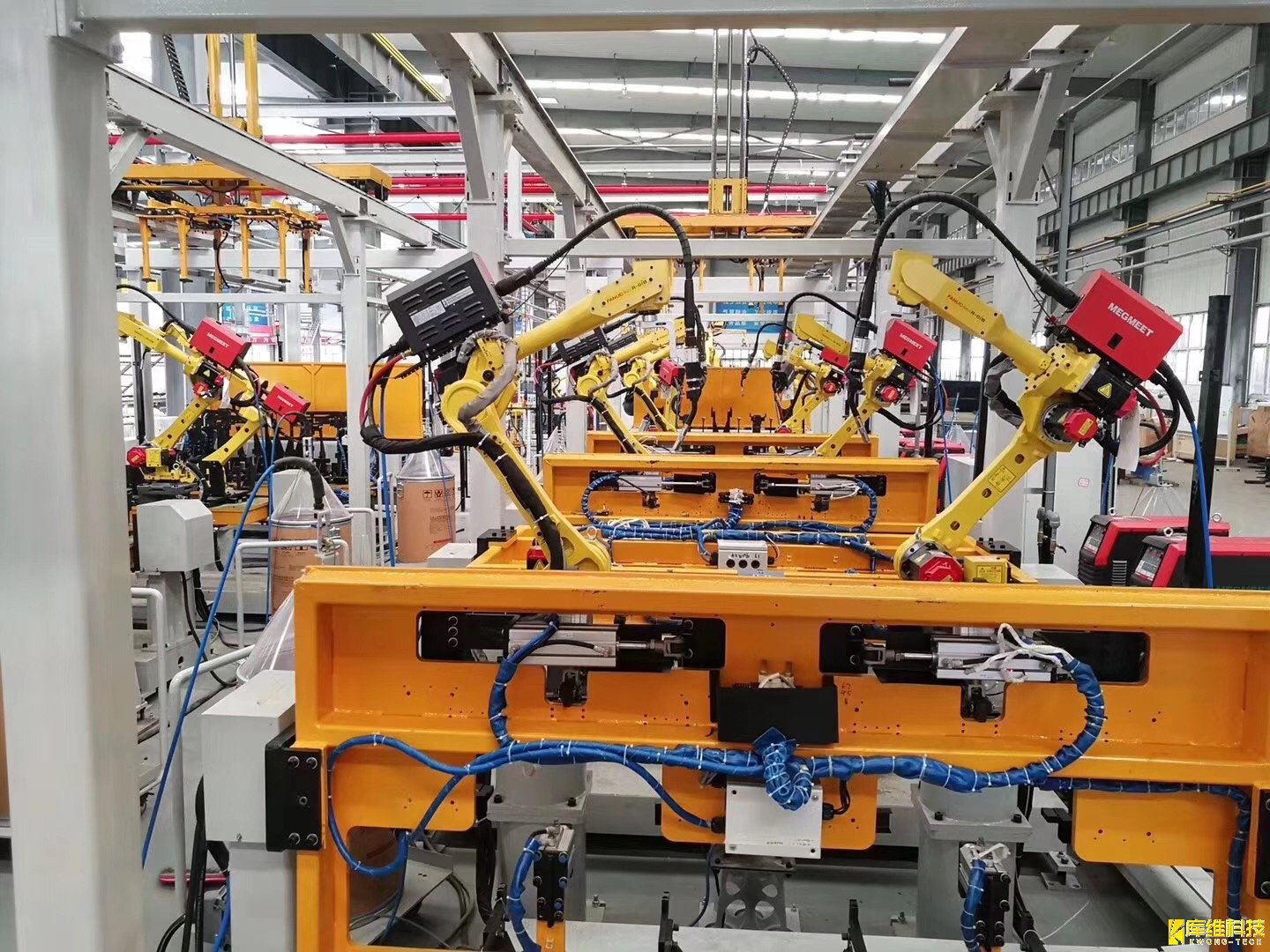
随着用工成本和技工不确定性风险的增加,自动化加工方式使用先进的技术使得该系统能够处理各种复杂形状的工件,并且保证了工件的加工质量和产品的一致性。自动化的生产加工方式已经越来越受到各行各业企业的认可。
实现方法:通过在机器人上的力反馈传感器,以及内置在设备中的专家参数库,结合工件与抛光轮之间的磨损消耗计算方程,使得系统能够实现复杂磨削,随形抛或安装三维数模尺寸抛都成为可能。力反馈补偿、自动计算磨损和补偿值,在线质量控制等功能,极大地提高了产品加工效率,并保证了加工工件的质量高度一致性。通过使用机器人自动化单元,不仅将产品质量提高一个档次,而且面对已经到了的高用工成本,技工基本技能不扎实等问题,制造企业都可以轻松应对。
1、实现了焊缝的全自动打磨抛光清理,完全解放了人工——在加工程序、智能软件系统、硬件系统的相互配合下,能充分实现焊缝的全自动打磨抛光,不需要人工辅助。
2、超高柔性、高度灵活、大大提高焊缝打磨效率——能至少替代10个工人,且能24小时连续不间歇高速工作,不受任何外界因素的干扰。打磨抛光稳定性好,产品一致性高。
3、超高人工智能性,能打磨抛光复杂曲面焊缝,充分保证焊缝打磨精度——能“观察”焊缝的尺寸、位置、特征,能“感知”焊缝表面受到力的大小,能根据各种数据反馈分析进行“智能调整”,充分保障了机身、车体、船体各种复杂不规则曲面焊缝打磨抛光的高精度。
4、加工程序支持离线编程,适合多种产品的焊缝打磨抛光,一机多用——加工程序支持离线编程,新型产品的焊缝打磨,离线即可启动加工程序,且此过程无需停机,减少了机器人的空转时间,保持工作连贯性,大大提高加工效率。
5、稳定性强,使用寿命长——优质的机器人本体关键部件采用国外进口,能充分保证机器人的运行稳定性,保证其使用寿命。售后,公司将会支持提供备件、耗材、高性价的打磨抛光工具,为机器人的正常使用保驾护航。
6、系统集成、联动性好——能和其他焊接、涂装设备之间通讯,实现无缝链接,组成智能生产线,提高效率,节约成本。
7、能打磨抛光各种材质——不锈钢、铝合金、钛合金、钢铁、镁铝合金等都可高效率打磨抛光,能充分满足机身、车体、船体焊缝打磨抛光需求。
8、现阶段当前当在金属制品生产中其普遍采用熟练工人利用电、气动研磨工具手工进行打磨抛光。
9、抛光打磨时产生总之易燃易爆粉尘,对个人人体而言一方面是风险因素危险。
10、当前每十年都市型有即使打磨抛光粉尘六所造成在我看来重大突发事件,这样的话可说是造成了极大的的人员财产损失。
11、能否避免该类生产事故再次出现。
12、要根本性解决这些问题便需要针对经济模式进行转型升级。
打磨抛光机械手适用于各种类型工件和材料磨削抛光工艺的各个方面,相对于机器人自动化磨削抛光的高效,常规复杂形状工件的抛光(如航空叶片,管件,水龙头,精密铸造件等)都需要由人工完成,人工打磨操作的主要缺点列举如下:
1、加工效率低、人工操作,会出现疲劳度的问题。
2、产品一致性难以保证,人工操作,会有熟练程度,技术水平的问题,难以保证加工工件的一致性。
3、生产人员工作环境恶劣,操作者总是处于噪音大,粉尘多的工作环境中,作业环境会对人体造成危害。
4、管理成本较高,工人工资成本较高。