激光打孔工艺在现代制造业中至关重要,但其参数优化一直是一个复杂的挑战。传统的试错法不仅耗时,而且成本高昂,因此亟需寻找更高效的优化方法。本文将探讨如何通过结合机器学习与分子动力学(MD)来实现飞秒激光打孔工艺的优化。
一、激光打孔的挑战
激光打孔的质量与多个参数密切相关,包括激光功率、频率和脉冲宽度等。虽然利用物理模型(如双温模型TTM和分子动力学MD)可以提供一定的理论支持,但在处理深孔等复杂问题时,传统模型往往难以进行有效的定量优化。
二、创新方法:分子动力学与机器学习的结合
为了解决传统方法的局限性,研究者们提出了一种新的过程优化框架,结合了分子动力学模拟、机器学习和高通量优化算法。该框架的关键步骤包括:
数据获取:通过分子动力学模拟获取丰富的物理信息,形成用于训练机器学习模型的数据集,从而减少了所需的数据量。
模型建立:机器学习快速准确地建立激光参数与目标加工性能之间的回归模型。
优化工艺:高通量优化算法确定最佳加工参数,以提高加工质量和效率。
三、实验验证
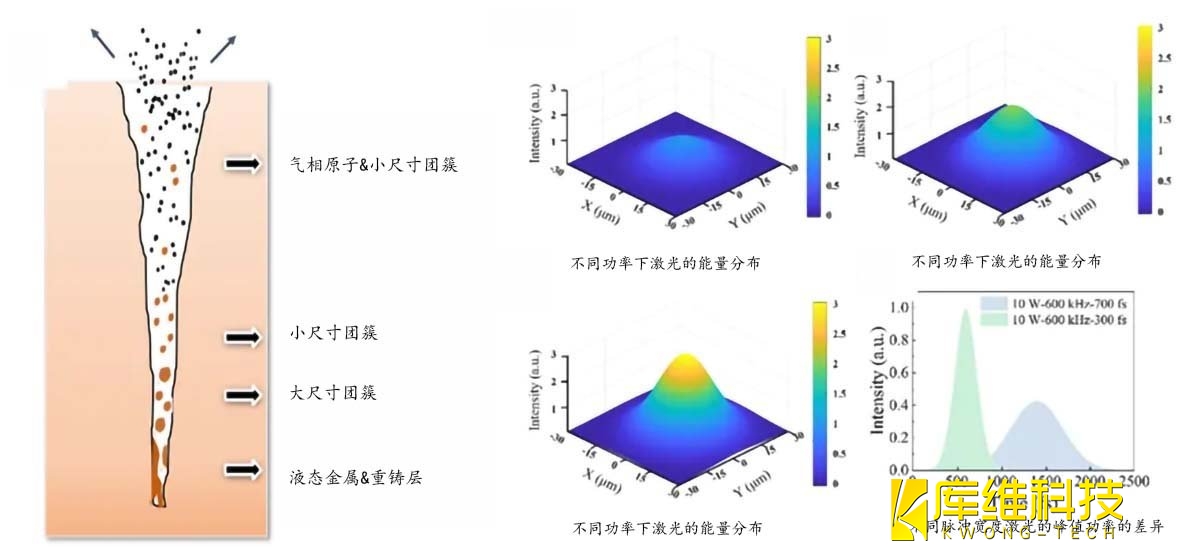
图中描述了烧蚀金属靶材的过程中的一系列行为以及展示了不同功率下激光的能量分布和不同脉冲宽度激光的峰值功率的差异。
图中(b)展示了通过分子动力学获取的参数在皮尔逊相关系数中的结果,LP为激光功率,F为频率,PW为脉冲宽度,CA为团簇数量,VAA为气相原子数量,CZ为团簇平均尺寸,AR为烧蚀率,RL为重铸层厚度,MRR为材料去除率。皮尔逊相关系数表明,绝对值越趋近于1的变量之间相关性越高。设置AR、RL和MRR为加工质量参数,图中可以看出,CA、VAA与加工质量结果密切相关,证明了MD获得的物理参数与加工效率和质量具有很高的相关性。图中(a)为烧蚀羽流中团簇和气相原子数量随时间的演化,图中(c-d)为模型对材料去除率的预测结果,图中(e-f)为模型对重铸层厚度的预测结果。
为了验证机器学习耦合分子动力学模型的有效性,设置了四种工艺。通过对镍基单晶高温合金的实验验证,四种打孔工艺的微孔截面的微观结构可以明显看出,采用机器学习耦合分子动力学的四步冲击式打孔工艺得到的微孔具有更薄的重铸层和更小的锥度,验证了优化工艺的有效性。
四、关键发现
提高预测精度:TTM-MD模型的引入有效提高了机器学习模型的预测精度,为工艺设计提供了可靠保障。
优化加工质量:基于机器学习的分阶段钻孔策略显著提升了微孔的质量和加工效率。
结合机器学习与分子动力学的飞秒激光打孔工艺优化方法,为激光材料加工领域提供了新的解决方案。通过实验验证,该方法的有效性得到证实,有望在微孔加工领域发挥更大作用。因此,机器学习引导的工艺参数不断变化的飞秒激光钻孔策略可能是优化微孔质量和效率的进一步研究方向。